SECTION A (40 marks)
Answer all the questions in this section.
-
- State one reason for teaching metalwork at secondary school level. (1 mark)
- List four components of a business plan. (2 marks)
-
- State four safety precautions to be observed when using bench shears in a workshop. (2 marks)
- Explain the importance of technical drawing in metalwork industry. (1 mark)
-
-
- Sketch and label an odd-leg calipers.
- State two uses of an odd-leg calipers. (3 marks)
- State five uses of the square head of a combination set. (2½ marks)
-
-
- Name three types of snips used in sheet metal and state the use of each. (3 marks)
-
- State four specifications to be considered when purchasing a rivet. (2 marks)
- Sketch a bifurcated rivet and state one use of the rivet. (1 mark)
-
- For each of the following items, name the material used and state one property of the material:
- ball pein hammer head; (1 mark)
- twist drill bit; (1 mark)
- body of an aircraft. (1 mark)
- List five methods of finishing metal articles. (2½ marks)
- For each of the following items, name the material used and state one property of the material:
-
- Explain the term "file cut". (1 mark)
- Name and sketch two types of file cuts. (2 marks)
-
- State two disadvantages of cooling a brazed joint rapidly. (2 marks)
- Explain the reason for tempering a cutting tool and outline the procedure of tempering. (3 marks)
-
- Explain one advantage of a forged bole over a drilled hole. (1 mark)
- Use a sketch to show the effect on the grain structure of a forged hole and a drilled hole. (2 marks)
- Use labelled sketches to show the following operations on a lathe machine:
- parallel turning; (1½ marks)
- facing off. (1½ marks)
- Explain each of the following terms as applied in arc welding:
- scratching; (1 marks)
- tapping; (1 marks)
- freezing (1 marks)
SECTION B (60 marks)
Answer question 11 and any other three questions from this section. Candidates are advised to spend
not more than 25 minutes on question 11.
- Figure 1 shows a truncated pipe of diameter 24 mm. Draw the development of part B. (15 marks)
(Use A3 paper provided) - Figure 2 shows an arc welding set-up.
-
- Name the parts labelled A, B, C, D, E and F. (3 marks)
- State the function of each of the following parts: B, C, D (3 marks)
- With reference to arc welding;
- Define the term bead; (1 marks)
- Outline the procedure of starting a bead. (5 marks)
- Use sketches to show the following defects in arc welding and state one cause of each. (3 marks)
- undercut;
- porosity.
-
- Figure 3 shows a drawing of a lathe machine.
- Name the parts labelled A, B, C, D, E and F and state one function of each part. (9 marks)
- State and explain four factors which determine the rate of material removal when turning on a lathe. (6 marks)
- With the aid of sketches, outline the steps followed in making a grooved seam joint of an open cylinder and name two tools used in each case. (15 marks)
-
- State four possible causes for each of the following:
- drill bit breakage; (2 marks)
- weak riveted joint. (2 marks)
- Figure 4 shows a working drawing of an engineer's trysquare drawn in first angle projection.
Given the cutting list below, outline the procedure of making the trysquare.
PART NO. OFF LENGTH (mm) WIDTH (mm) THICKNESS (mm) MATERIAL Stock (B) 2 63 22 4.5 BDMS Blade (A) 1 95 70 1.5 BDMS Rivets 3 14.5 - Φ3 BDMS
(11 marks)
- State four possible causes for each of the following:
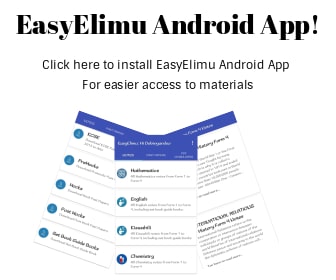
MARKING SCHEME
SECTION A
-
- Reasons for teaching metalwork Secondary school level.
- To equip learners with knowledge, skills and attitudes relevant to the field to enable them pursue further training.
- To enable the graduate student enter into gainful self or salaried employment after training,
Any 1x1 = 1 mark
- Components of a business plan..
- Executive summary
- Marketing
- Management and organizational
- Production/ operation
- Financial plan/ budget
Any correct 4 x ½ = 2 marks
- Reasons for teaching metalwork Secondary school level.
-
- Safety precautions to be observed when using bench shears:
- Always return hand to its normal position so as not to obstruct workshop users.
- Use to cut the recommended size of materials.
- The shears should be firmly fixed onto the bench.
- The jaws of the shears should be sharp enough.
4 x ½ = 2 marks
- Importance of technical drawing in metalwork industry
- To enable the design and fabrication of articles.
- To enable people in the industry interpret existing drawings.
Any 1 x 1 = 1 mark
- Safety precautions to be observed when using bench shears:
-
-
- Odd-leg callipers
Sketch - 1 mark
Labelling any 2 x ½ = 1 mark - Uses of odd-leg callipers
- Scribing parallel lines
- Locating centres
2 x ½ = 1 mark
Total = 3 marks
- Odd-leg callipers
- Uses of square head of a combination set.
- Marking lines square to an edge.
- Testing for squareness.
- Marking out and checking depths.
- Marking of 45°
- Checking for 45°
- Checking the flatness of a workpiece using its spirit level.
5 x ½ = 2½ mark
-
-
- Types of snips and their use:
- Straight type - used for cutting straight edges
- Curved type - used for cutting internal curves
- Universal type - used for cutting almost any shape.
Types - 1½marks
Uses - 1½ marks
Total = 3 marks
-
- Specifications to be considered when purchasing a rivet
- shark diameter
- shark length
- material used
- type of head
4 x ½ = 2 marks
- Sketch a bifurcated rivet.
Used for leather work
Sketch - ½ mark
Use - ½mark
Total = 1 mark
- Specifications to be considered when purchasing a rivet
- Types of snips and their use:
-
- Materials used for:
- ball pein hammer - medium carbon steel (M.C.S)
Property - it is tough - twist drill bit - high carbon steel (H.C.S)
Property - it is hard and resists wear - Body of aircraft - Aluminium alloy
Property - it is light, strong and non-corrosive.
Naming material - 3 x ½ = 1½
Property - 3 x ½ = 1½
Total = 3 marks
- ball pein hammer - medium carbon steel (M.C.S)
- Methods of finishing metal articles
- brush painting
- spray painting
- bluing
- oil blacking
- laquering
- etching
- planishing
Any 5 x ½ = 2½ marks
- Materials used for:
-
- File cut means the formation of the teeth of a file. (1 mark)
- Types of file cuts
Naming any 2 x +½ = 1 mark
Sketching any 2 x ½ = 1 mark
(other types not shown to be accepted) Total = 2 marks
-
- Disadvantages of cooling a brazed joint rapidly:
- The joint ends up being weak
- Scaling is caused
- The joint may crack
- There is interference with the grain structure.
Any 2 x 1 = 2 marks
- Reasons for tempering a cutting tool is to remove brittleness/ excessive hardness and increase toughness.
(1 mark)
Procedure for tempering:- Clean the work piece
- Heat the tool away from the cutting edge/point
- Observe the tempering colour while heating
- Quench appropriately
4 x ½ = 2 marks
- Disadvantages of cooling a brazed joint rapidly:
-
- Advantage of a forged hole over a drilled one. The grain flow strengthens the hole structure. 1x1 = 1 mark
-
- Operations on a lathe machine
- Parallel turning
3 x ½= 1½ marks - Facing
- Parallel turning
- Terms of arc-welding
- Scratching is a method of striking an arc by scratching
- Tapping is a method of starting an arc where the electrode is brought down until it is in contact with the metal to be welded.
- Freezing is the tendency of the electrode to stick on the metal being welded.
1x 3 = 3 marks
SECTION B
- Figure shows a truncated pipe of diameter 24 mm.
ACCEPT ALTERNATIVE OPENING POINT -
-
- Naming parts labelled
A - metal core
B - Flux/electrode covering
C - Gaseous shield
D - Slag
E - Globules of molten core wire
F - Parent metal
6 x ½ = 3 marks - B-The flux has the following functions:
- enable the are to be struck and maintained easily.
- floats the impurities out of the molten metal to form the slag.
- provides iron powder to increase the rate of depositing.
- it forms a layer that makes the joint to cool slowly.
Any 1x l = 1 mark
- C-The gaseous shield has the following functions:
- it helps protect the weld.
- it slows down the cooling of the joint.
Any I x 1 = 1 mark
- D-The slag is the uniformly deposited molten electrode which forms the joint for decorative purposes.
(1 mark)
- Naming parts labelled
-
- The term bead refers to the pattern formed in the welding process. 1x1 = 1 mark
-
- Prepare the plate to be welded
- Draw the required path of the bead with a piece of chalk
- Position the work ready for welding - earth the workpiece
- Select the correct electrode.
- Set the correct welding current.
- Add the electrode slanting at an angle of 75° in the direction of travel.
- Wear protective gear.
- Strike the arc.
- Momentarily raise the electrode after establishing the are.
- Lower the electrode to the correct are length.
- Start building up the desired bead.
10 x ½ = 5 marks
- Defects in arc welding
- Undercut
Figure 6
Causes:- Use of excessive current Sketch - 1 mark
- Improper angle of electrode to the base metal. Any 1 cause - ½ mark
- Porosity
Figure 7
Causes- Excessive moisture in the electrode or joint.
- High rate of metal freezing.
- Oil, paint or rust on the surface of the base metal.
- Improper arc length, current or manipulation.
Sketch - 1 mark
Any 1 cause -½mark
1½ marks
- Undercut
-
-
- A Head stock - carries the driving mechanism
B Headstock spindle - hold the chuck or live centres
C Bed - supports the carriage and tailstock
D Dead centre - supports the tailstock
E Tail stock - for feeding the drills
for securing the work
F Tool post - holds the cutting tool
correct name 6 x½ = 3
correct function 6 x 1 = 6
Total = 9 marks - TYPE OF FINISH - Fine finish will require slight cut.
Rough finish will require deep cut.
HARDNESS/SOFTNESS - Soft material require deep cut.
- Hard materials slight cut.
TOOL - ANGLE - round nosed up for heavy cut pointed tip for light cut.
MACHINE STABILITY. Stable allows deep cut unstable for light cut.
RIGIDITY OF CUTTING TOOL - Rigid for deep cut, unrigid for light cut.
Stating any 4 x ½ = 2 marks
Explaining any 4 x 1 = 4 marks
6 marks
- A Head stock - carries the driving mechanism
- Steps followed in making a grooved seam joint of an open cylinder
Steps Sketch Tools used- Mark out seam allowances
- Try square
- Steel rule allowances
- Scriber - Bend the flaps
- Folding bars
- Mallet - Fold both sides to same size
- Anvil
- Mallet - Hook the ends and tighten the joint
- mallet
- anvil/stake - Close down or groove the joint
- Hammer
- Stake
- Groover
Steps well outlined = 5 marks
Sketches 5 x 1 = 5 marks
Tools 5 x 2 x ½ = 5 marks
Total = 15 marks
- Mark out seam allowances
-
-
- Causes of drill breakages
- too high feed rate.
- speed too high
- incorrect alignment.
- drill jamming in the hole.
- workpiece not properly clamped.
4 x ½ = 2 marks
- Causes of weak riveted joint
- too short rivet head allowance
- too large hole diameter
- gap between plates/failure to deburr close plates.
- misaligned holes.
- too long rivet allowance.
4 x ½ = 2 marks
- Causes of drill breakages
-
- Stock
- file datum edges
- mark out rivet holes
- centre punch holes position
- debur
4 x ½ = 2 marks
- Blade
- file datum edges
- mark out profile
- cut out profile
- file profile to size
- mark out blade hole
- centre punch hole
- drill hole
- mark out stock position (6 mm)
8 x ½ = 4 marks
- Assembling the parts
- align and clamp the two parts together.
- drill through and put the rivers in the holes.
- drill the remaining rivet holes.
- countersink the holes.
- deburr the plates/parts.
- insert rivets and close plates.
- rivet to fill the countersunk holes.
- file all surfaces to size.
- mark and cut out notch.
- finish with emery cloth.
10 x ½ = 5 marks
- Stock
-
Download KCSE 2012 Metalwork Paper 1 with Marking Scheme.
Tap Here to Download for 50/-
Get on WhatsApp for 50/-
Why download?
- ✔ To read offline at any time.
- ✔ To Print at your convenience
- ✔ Share Easily with Friends / Students